How to Build a Warehouse: Complete Project Planning and Construction Guide
Posted by: admin on March 10, 2025
Constructing a new warehouse demands more than just erecting walls and installing shelves. Proper planning, strategic budgeting, and detailed project management shape the difference between a successful build and costly setbacks. Facility owners who anticipate these challenges from the start avoid expensive delays and maximize their long-term investment. Every warehouse forklift operator, site manager, and project leader must be prepared well before breaking ground to ensure the best outcomes.
Building a Warehouse Successfully
Before construction begins, understanding how each phase interlocks is critical. Setting clear objectives, choosing the right construction partners, and maintaining open communication throughout the build avoids missteps. Many projects fall behind schedule due to overlooked details or poor pre-construction organization. By following a step-by-step warehouse project planning approach, teams can steer projects to timely completion and safer operations.
Step 1: Set Clear Warehouse Project Goals
Clarifying warehouse project objectives starts the build off on the right track. Define the primary use of the facility: whether it will serve storage, manufacturing, fulfillment, or multi-purpose needs. Specific goals regarding building size, ceiling height, loading dock capacity, and specialized workspaces guide later design decisions. Setting measurable goals like square footage targets, occupancy dates, and operational workflows eliminates scope creep.
Step 2: Create a Realistic Warehouse Budget
Drafting a complete and flexible budget anchors project decisions. Include estimates for land purchase, excavation, permitting, design services, and construction materials. Labor costs fluctuate depending on location, timeline urgency, and available contractors. Plan for 10–20% additional funds beyond core costs to cover surprises such as site issues, change orders, or delays. Upfront planning strengthens financial resilience throughout the build.
Step 3: Building a Warehouse Checklist
A detailed checklist provides a roadmap for efficient warehouse construction:
- Site Selection: Soil testing, proximity to logistics hubs, zoning approvals
- Warehouse Layout: Racking systems, equipment aisles, inventory flow mapping
- Material Handling Equipment: Evaluating needs for forklifts, conveyor belts, pallet jacks
- Utilities and Infrastructure: Installing proper electrical, plumbing, internet, HVAC systems
- Fire and OSHA Compliance: Sprinkler system design, emergency exits, signage, lighting
- Expansion Planning: Designing scalable solutions for future warehouse growth
Step 4: Warehouse Construction Tips for Success
Efficient warehouse builds require careful pre-construction preparation. Clear the land fully before starting foundation work. Vet contractors by checking references, insurance policies, and project portfolios. Establish a realistic construction timeline with key milestones to monitor progress. Weekly safety briefings help keep teams aligned on OSHA compliance and job site hazard prevention.
Step 5: Key Considerations for Warehouse Project Planning
Organizing documents before construction starts accelerates project timelines. Secure building permits, zoning clearances, fire department approvals, and environmental impact assessments early. Understand that warehouse size affects average build time—smaller warehouses under 10,000 square feet often take 3–6 months, while larger distribution centers may require 9–18 months. Managing change requests efficiently keeps timelines intact without blowing the budget.
Cost to Build a Warehouse: What to Expect
Typical warehouse construction costs range from $20 to $40 per square foot depending on design complexity and material choices. Pre-engineered metal buildings (PEMBs) represent the most affordable option, while custom concrete tilt-up facilities cost more. Key factors that influence warehouse construction expenses include:
- Land preparation difficulty
- Material shortages and supply chain impacts
- Labor market conditions
- Facility amenities like climate control and office space
Small basic warehouses may cost $150,000–300,000. Mid-sized distribution facilities often range $500,000–1.2 million. Mega warehouses and fulfillment centers can exceed several million dollars easily.
FAQs About Building a Warehouse
How Long Does It Take to Build a Warehouse?
Small warehouses typically take 3–6 months. Larger, highly customized facilities may require up to 18 months from ground-breaking to ribbon-cutting.
How Much Does a 10,000 Sq Ft Warehouse Cost?
Expect basic shell construction of a 10,000 sq ft warehouse to run between $200,000 and $400,000 depending on build complexity and location.
What Permits Are Needed to Build a Warehouse?
Building permits, zoning approvals, fire department inspections, environmental impact studies, and OSHA workplace readiness certifications are commonly required.
What Equipment Is Needed Once a Warehouse Is Built?
Essential equipment includes warehouse forklifts, pallet racking, conveyor systems, pallet jacks, packaging stations, scales, and fire suppression tools.
Build Warehouse Safety from the Ground Up with CertifyMe
CertifyMe delivers fast, affordable OSHA forklift training tailored for warehouse environments. Before stocking the first pallet or moving inventory, ensure every warehouse forklift operator holds up-to-date certification. Our online programs offer 24/7 access, immediate proof of training, and free three-year renewals to keep your warehouse OSHA-compliant and accident-free from day one.
Welcome to CertifyMe.net
CertifyMe.net has offered online forklift certification since 1999. With Our Convenient online program. your employess can earn their certification in an hour or less.
Browse Online Certifications:
This low-cost program can be compeleted anytime, anywhere!
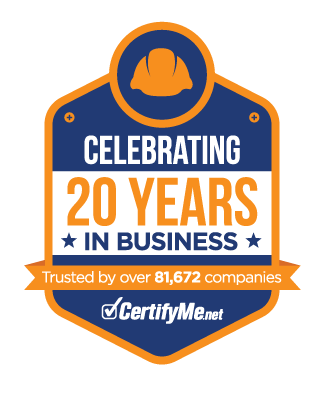
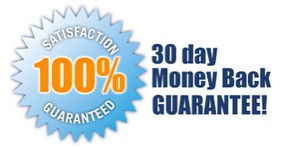