OSHA Forklift Checklist 2025: A Step-by-Step Guide to Full Compliance
Posted by: admin on April 29, 2025
Forklifts help keep operations moving, but improper training and documentation can put your entire business at risk. OSHA’s Powered Industrial Trucks Standard (29 CFR 1910.178) lays out exactly what’s required to stay compliant—and safe.
This guide is built for safety managers, HR leaders, and operations professionals who need a clear, practical roadmap to forklift compliance. Let’s break it down section by section.
1. Who Needs Forklift Certification?
The first step to compliance is identifying everyone who operates a powered industrial truck (PIT). Many companies make the mistake of assuming only full-time drivers need certification.
Make sure to:
-
Include all operators of forklifts, pallet jacks, reach trucks, and order pickers.
-
Count full-time, part-time, seasonal, and temporary workers—OSHA does not differentiate by status.
-
Cross-check job descriptions with actual job duties.
-
Review departments regularly to identify changes in responsibilities.
Why it matters: Allowing uncertified employees to operate equipment puts your business at risk of OSHA citations and legal consequences in the event of an accident.
2. Administrative Compliance
OSHA inspectors don’t take your word for it—they want to see the paper trail. That means your forklift safety program must be documented, organized, and accessible.
What to have in place:
-
A written forklift safety policy outlining training, operation procedures, and recertification schedules.
-
OSHA-compliant signage and safety rules posted where forklifts are in use.
-
A centralized tracking system for certifications and expiration dates.
-
Automated reminders to prevent certification lapses.
-
A detailed training log for each operator, including dates, trainer credentials, and equipment used.
Pro tip: Go digital. Manual tracking is risky, and lost paperwork can cost you during an inspection.
3. Training Requirements
Forklift training is more than checking a box. OSHA requires that training includes formal instruction, practical application, and a performance evaluation.
Training must cover:
-
Operating instructions, safety precautions, and warning labels.
-
Key differences between PITs and regular vehicles.
-
Controls, instrumentation, and braking systems.
-
Refueling, battery charging, and maintenance basics.
-
Load handling and stability principles.
-
Visibility limitations and operational restrictions.
-
Environmental factors like ramps, surfaces, and pedestrian zones.
-
Worksite-specific hazards and safety procedures.
Common mistake: Using generic, one-size-fits-all training. OSHA expects content that’s relevant to your specific workplace and equipment.
4. Evaluation and Certification
Certification is only valid when operators pass an on-site, hands-on performance evaluation conducted by a qualified trainer.
Requirements include:
-
Evaluation on the specific equipment type (e.g., sit-down vs. stand-up forklifts).
-
Completion of the evaluation by a certified trainer—not a peer or supervisor without formal training.
-
Issuing a signed certificate with operator name, date, trainer credentials, and equipment type.
-
Storing certificates and evaluations in an easily retrievable system.
Tip: Use an equipment matrix to track which operators are certified for which models.
5. Recertification and Re-Evaluation
OSHA mandates recertification every three years, but earlier training may be necessary based on performance or job changes.
Retraining is required when:
-
An operator is observed using equipment unsafely.
-
A forklift-related accident or near miss occurs.
-
The operator is assigned a new type of PIT or work environment.
Best practice: Use a rolling schedule to avoid last-minute lapses or mass expirations.
6. Documentation and Retention
Records are your legal shield. Without them, you’re unprotected during audits or accident investigations.
Each record should include:
-
Employee name and ID
-
Training type and dates
-
Trainer name and qualifications
-
Equipment used in training
-
Evaluation results
Organize files by site and department, and retain them for a minimum of three years. Cloud-based systems prevent data loss and ensure access when needed.
7. Equipment and Site Safety
Even the most skilled operator can’t prevent accidents caused by faulty equipment or unsafe conditions.
Conduct pre-shift inspections, checking:
-
Tires, brakes, and fluid levels
-
Warning lights, alarms, and horn
-
Seatbelts, load backrest, and safety features
Immediately tag and remove equipment from service if it fails inspection. Maintain detailed maintenance records to show ongoing compliance.
8. Building a Strong Safety Culture
Compliance is the baseline. Creating a safety-first culture is how you build long-term success and reduce incident rates.
Best practices include:
-
Monthly safety meetings and toolbox talks
-
Anonymous channels to report concerns
-
Near-miss tracking and follow-ups
-
Recognizing and rewarding safe behavior
-
Leadership involvement in safety initiatives
Culture tip: Safety grows when it’s owned by everyone—not just the safety team.
Take the Next Step Toward OSHA Compliance
Manual compliance tracking eventually breaks down—especially across multiple sites or teams.
CertifyMe.net makes it easy to stay compliant with:
-
Certification tracking
-
Automated renewal reminders
-
OSHA-ready documentation
-
Role-based dashboards
Don’t let training gaps or paperwork failures put your business at risk. Build a forklift program that’s efficient, compliant, and bulletproof.
Welcome to CertifyMe.net
CertifyMe.net has offered online forklift certification since 1999. With Our Convenient online program. your employess can earn their certification in an hour or less.
Browse Online Certifications:
This low-cost program can be compeleted anytime, anywhere!
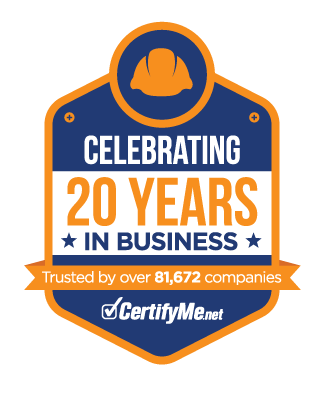
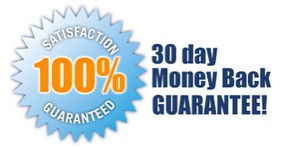