How to Handle Forklift Repairs: Troubleshooting and Maintenance Tips
Posted by: admin on March 31, 2025
Forklift breakdowns create costly delays, safety hazards, and unexpected expenses. Addressing forklift repairs proactively through regular maintenance is essential for keeping operations smooth. Proper upkeep not only extends the forklift lifespan but prevents expensive emergencies that can shut down a warehouse.
Why Timely Forklift Repairs Are Critical
Forklifts endure intense daily use, leading to wear and tear across hydraulic, steering, and mast systems. Ignoring early warning signs risks cascading failures, much higher repair bills, and potential safety incidents. Regular troubleshooting and prompt repairs protect both workers and equipment while reducing unplanned downtime.
What Are the Most Common Forklift Repairs?
Mast Problems
Forklifts that lift jerkily or lower too slowly often signal mast issues. Hydraulic fluid levels or worn chains usually cause these symptoms. Routine checks of both can catch problems early before they escalate into system failures.
Steering Problems
Tight spaces amplify steering challenges. Noises while turning or difficulty controlling the forklift suggest possible hydraulic leaks, loose valves, or worn gears. Immediate inspection prevents steering-related accidents and costly damages.
Starting Problems
Forklifts refusing to start typically suffer from drained batteries, clogged fuel lines, or old fuel. Verifying battery charge and checking for coolant or radiator problems ensures that starting issues do not derail operations.
Forklift Troubleshooting Guide: Step-by-Step Process
Mast Problems and Repairs
- Inspect hydraulic fluid levels.
- Examine mast chains for cracks, stretches, or corrosion.
- Replace damaged sections promptly to avoid bigger malfunctions.
Steering Problems and Repairs
- Check steering fluid and refill if necessary.
- Replace fluid if it appears contaminated or thick.
- Have a qualified technician inspect gears and hydraulic valves.
Starting Problems and Repairs
- Recharge or replace the battery.
- Inspect fuel systems for leaks or blockages.
- Check coolant levels and radiator condition.
How to Build a Forklift Maintenance Checklist
A structured forklift maintenance checklist helps catch issues early and prevents costly repairs.
- Daily Checks: Inspect tires, fluid levels, warning lights, and basic controls.
- Weekly Checks: Examine mast systems, hydraulic hoses, and steering components.
- Monthly Checks: Service battery systems for electric forklifts, or engine and fuel systems for combustion models.
Warning Signs That Demand Immediate Forklift Repairs
Certain forklift issues demand urgent attention:
- Visible hydraulic leaks
- Malfunctioning or soft brakes
- Persistent dead battery issues
- Load instability during lifting or transport
Addressing these early can prevent accidents and save thousands in repair and liability costs.
Why Timely Forklift Repairs Protect Your Business
Investing in prompt forklift repairs avoids larger breakdowns, minimizes costly downtime, and keeps warehouses safe. OSHA violations from poorly maintained equipment can result in fines or operational shutdowns. Proper maintenance builds reliability into every shift, improving productivity and protecting both workers and assets.
FAQs About Forklift Repairs
How Do You Repair a Forklift Mast?
Maintaining proper hydraulic fluid levels and replacing worn chains typically resolves most mast lifting and lowering problems.
What Is the Most Common Cause of Forklift Breakdowns?
Neglected maintenance—especially low fluid levels—remains the leading cause of unexpected forklift failures.
How Often Should Forklift Troubleshooting Occur?
Forklifts should undergo daily visual inspections, weekly functional checks, and monthly deeper service reviews to maintain peak performance.
Can Untrained Employees Repair Forklifts?
No. OSHA requires that forklift repairs must only be completed by trained and qualified maintenance personnel to ensure safety compliance.
Extend Forklift Life and Reduce Repairs with CertifyMe
CertifyMe offers fast, OSHA-compliant forklift training that empowers operators to spot early signs of equipment issues. Our online certification courses reinforce maintenance best practices while boosting warehouse safety and performance. Gain 24/7 access, instant proof of training, and free three-year renewals when you certify your team through CertifyMe.
Welcome to CertifyMe.net
CertifyMe.net has offered online forklift certification since 1999. With Our Convenient online program. your employess can earn their certification in an hour or less.
Browse Online Certifications:
This low-cost program can be compeleted anytime, anywhere!
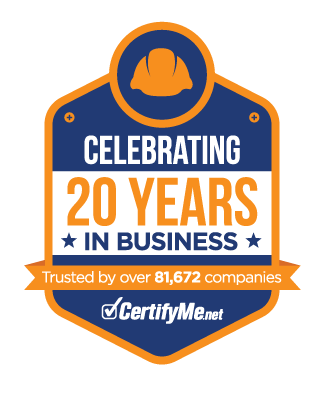
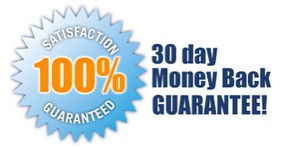